
|

|
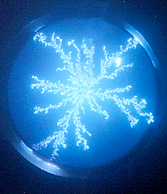
|
BESCHICHTUNG
|
|
Hartstoffbeschichtung
Die von INOVAP
hergestellten PVD-Hartstoffschichten zeichnen sich durch eine feine Multilayerstruktur aus. Sie werden mit dem PulsArc-Verfahren hergestellt. Das PulsArc-Verfahren
ist eine neue PVD-Technologie, bei der die Elektronenemission und die
Plasmadichte am Substrat durch kontrollierte Hochstrompulse vervielfacht wird.
Dadurch werden Schichten mit
verbesserten Verschleißeigenschaften und geringerer Rauigkeit abgeschieden.
Die neue Technologie zeichnet sich durch eine hohe Prozessstabilität und
einfache Handhabung aus.
Beschichtungen
mit Hartstoffen wie TiN, TiAlN,
TiCN und CrN zeichnen
sich durch folgende Eigenschaften aus:
•
|
Die hohe Härte wirkt dem Abrieb entgegen
und verringert z.B. den Freiflächen- und Kolkverschleiß an Bohr- und
Fräswerkzeugen.
|
•
|
Hartstoffschichten verringern die Neigung der Werkzeuge,
zu verkleben oder zu verschweißen, deshalb bleiben die Schneidkanten und
Funktionsflächen länger frei von Aufbauschneiden und Kaltverschweißungen.
|
•
|
Die verringerte Reibung zwischen dem beschichteten Werkzeug und
dem Werkstück reduziert die Schnitt- und Umformkräfte.
|
•
|
Hartstoffschichten sind chemisch hochbeständig und
reaktionsträge, so bleibt die Funktionsfläche Ihres Werkzeuges länger
einsatzfähig.
|
•
|
Gute Haftung auf dem Werkzeug und quasi-elastisches Verhalten
der Hartstoffschichten reduzieren die Gefahr von Abplatzungen, Rissen und
Ausbrüchen an Schneidkanten und Funktionsflächen auch bei starken
Pressungen und hohen Schnittkräften.
|
Auf Grund der oben genannten Wirkungen ermöglicht der Einsatz
hartstoffbeschichteter Werkzeuge längere Standzeiten der Werkzeuge, eine
bessere Auslastung des Maschinenparks, höhere Bearbeitungsgeschwindigkeiten,
präziser bearbeitete Oberflächen, eine höhere Maßhaltigkeit der Werkstücke
sowie eine deutliche Verringerung von Rüst- und Justierzeiten.
|
Schichttypen
und Rezepturen
Für Werkzeuge aus
HSS, HM, VHM und Cermet
|
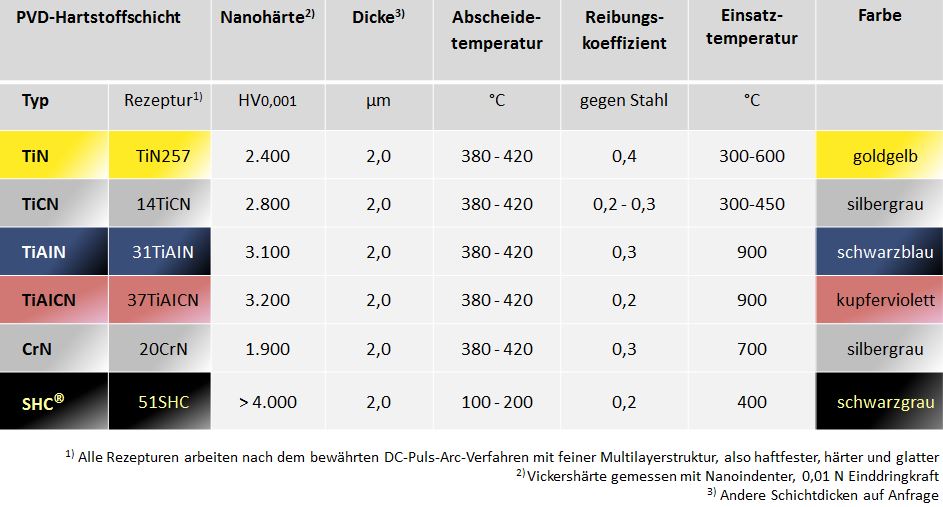
|
Anwendung
und Nutzen
Für Werkzeuge aus HSS, VHM, HM und Cermets
|
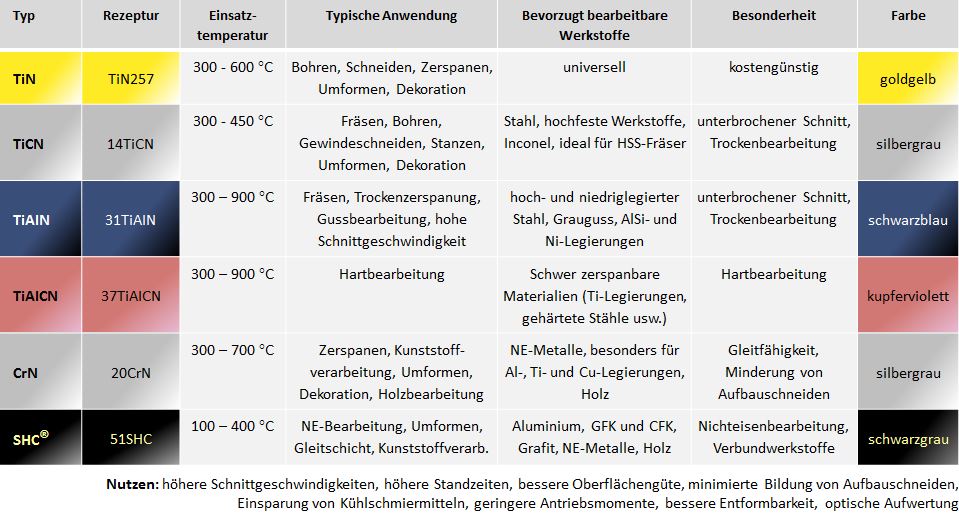 |
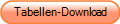
|
Schichtdickenmessung
mit dem
KALOTTENSCHLEIFGERÄT-KSG 110
|
|
|
Mit dem Kalottenschleifgerät
KSG 110 können bis zu 10 Kalotteneinschliffe unter
exakt definierten Prüfbedingungen automatisch nacheinander und mit
vorprogrammierten Parametern hergestellt werden.
|
|
|
Schematischer Querschnitt – Aufsicht im Lichtmikroskop
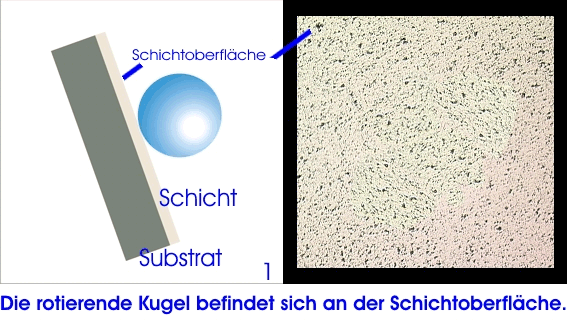
|
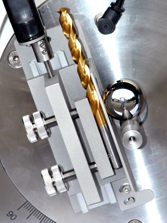
|
Die Kalo-Einschliffe liegen dicht nebeneinander und in einer
Reihe auf der Messfläche, so dass sie unter dem Mikroskop leicht
wiedergefunden und rasch vermessen werden können.
Die Einschleifparameter (Drehgeschwindigkeit,
Anzahl der Umdrehungen für jeden Einschliff, Abstand der Einschliffe auf der
Probe) werden an der Steuereinheit voreingestellt und von einer SPS digital
überwacht.
Die Steuereinheit übernimmt auch die Berechnung der Schichtdicke und der
Eindringtiefe.
Für die Bestimmung der Schichtdicke kann entweder der beste Einschliff
ausgewählt werden (Eindringtiefe, Schärfe der Messkanten, Rundheit), oder das
Messergebnis wird über mehrere Einschliffe gemittelt.
Daraus resultieren Messwerte von hoher Zuverlässigkeit und geringer
Standardabweichung. Durch die robuste Ausführung in Edelstahl ist das KSG 110
sowohl für den Laboreinsatz als auch für raue Produktionsumgebung
hervorragend geeignet.
Bei Kalo-Verschleißeinschliffen können die
Entwicklung des Verschleißkoeffizienten über den Verschleißweg und die Tiefe
der Einschliffe bestimmt werden. Auch kaum sichtbare Kalo-Einschliffe
geringer Tiefe können leicht gefunden und vermessen werden, da alle
Einschliffe in einer Reihe nacheinander angeordnet sind.
|
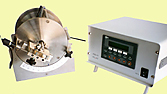
Technische Daten
•
|
Einstellbare Auflagekraft FN:
0 - 0,32 N (Stahlkugel Drm. 20 oder 30 mm); 0 -
0,63 N (WC-Kugel Drm. 20 mm)
|
•
|
Anstellwinkel: 0 - 90°
|
•
|
Drehzahl: 50 - 5000 min-1
|
•
|
Umdreh. bis: 1000000 U/Einschliff
|
•
|
Messpunkte/Probe: bis 10
|
•
|
Angezeigte Ergebniswerte:
Schichtdicke in µm; Tiefe des Kalotteneinschliffes
in µm
|
•
|
Berechnung: Verschleissvolumen
in mm3; Verschleisskoeffizient in m3/Nm
|
|